The intersection of IoT devices with 5G connectivity is already reshaping manufacturing, and is now widely recognised as a defining enabler of the Fourth Industrial Revolution. 5G IoT can serve the business drivers of manufacturers across the value chain – from raw materials and processing, to the factory floor itself, and all the way to logistics and distribution among customers. Diagnostics, tracking, connected tools, remote monitoring, and predictive maintenance are among the principal areas of interest to the manufacturing sector – while the data accrued from these use cases can further refine business processes, and develop new ones. Real-time image processing for instance can help spot defective items before they even make it off the production line, and then inform approaches to fresh production thereafter. In short, digitisation is set to create far more flexible, efficient and sustainable production lines – and 5G IoT will underpin this transformation by giving manufacturers vastly improved visibility and control over all aspects of their business.
The increasing interest in such solutions means there are immense and growing commercial opportunities at hand for the mobile industry: research by GSMA Intelligence finds a total of 2 billion IoT connections serving Industry 4.0 use cases will be online by 2025 (), a three-fold increase on the 660 million last year – 18% of which will be licensed cellular. 10% of Industry 4.0 revenues will come from providing connectivity alone, and MNOs as a whole can expect to take around 14% of the total revenue base of $13 billion as a base case scenario. Industry 4.0 was naturally a focus at MWC Barcelona this year, with a dedicated session bringing together senior experts from leading operators, manufacturers and OEMs to share their assessments of where we are in this exciting growth area.
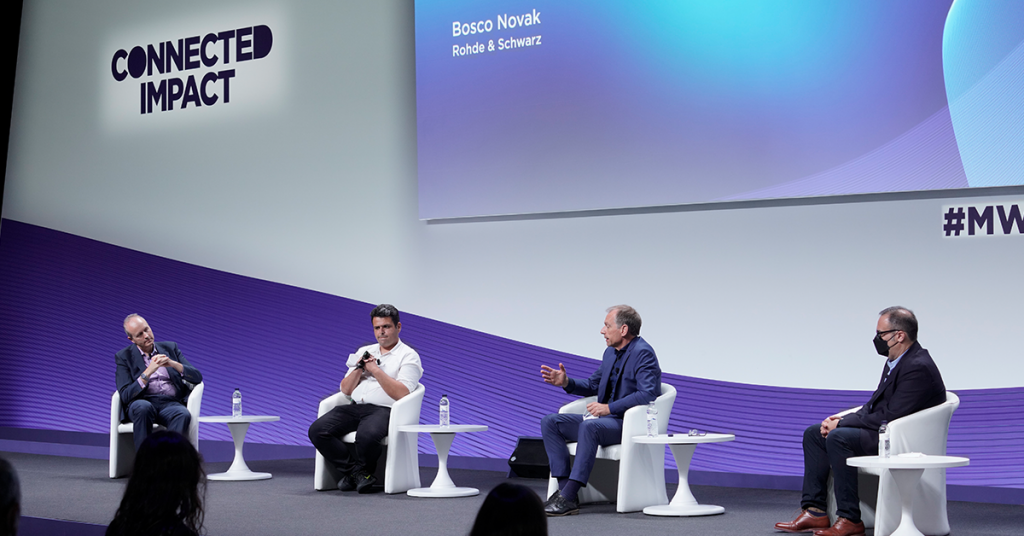
The GSMA works closely with manufacturers of almost all kinds, in particular through the 5G IoT Manufacturing Forum, which brings together players from across the mobile and manufacturing ecosystems to share knowledge and accelerate common problem-solving. The manufacturers we speak to consistently emphasise the importance of secure, reliable and scalable networks to maximise productivity. Rising demand for data-rich services means guaranteed bandwidth is an essential part of moving towards automation, and with real-time decision-making now crucial to the advent of Industry 4.0, ultra-low latency too is key. “We define fourth industrial revolution as the combination of interconnection, information transparency, high technical assistance and decentralised decision-making,” said Elise Neel, VP for New Business Incubation at Verizon, “through AI, connected devices, AR/VR, additive manufacturing, autonomous vehicles and robots. 5G’s role is to help connect, manage, operate and control the elements required to create an autonomous world; 5G is foundational for Industry 4.0 because you can’t create an interoperable system to manage that much data reliably, securely and at speed with Wi-Fi or even 4G.”
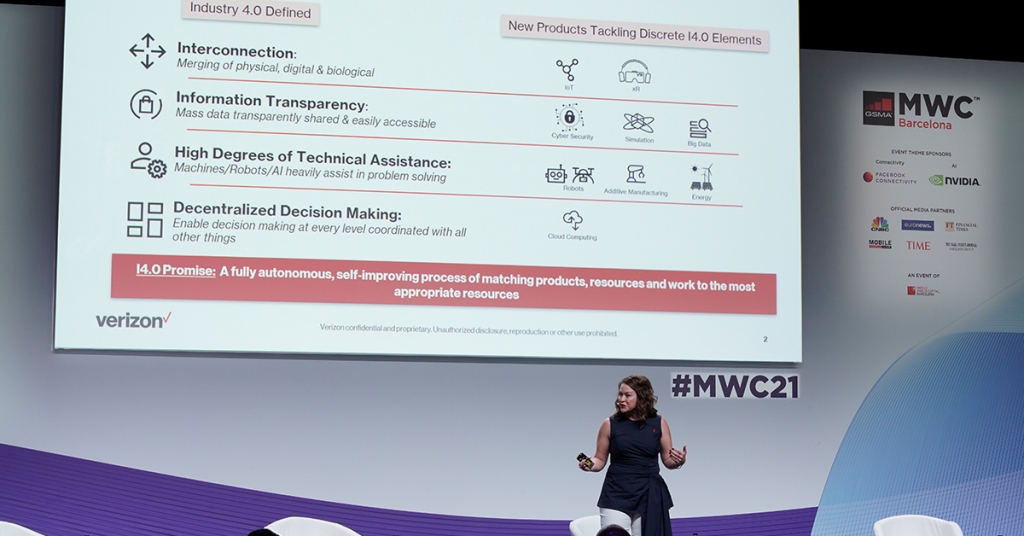
As Elise explained, when in the past industry has sought to connect large numbers of devices to reliable networks, the need has traditionally been met with hardwired solutions, making implementation long, complex and often expensive. If Industry 3.0 was about connecting industry, Industry 4.0 is in part about making it interconnected – enabling the interoperability required to make the most of the growing technological complexity involved, and ensure integrated solutions, rather than potentially inefficient and fragmented digitisation drives. Where individual OEMs focus on their own vertically integrated digital transformation programmes, for instance, they may not be conscious of the vast commercial potential of an ecosystem of sharing and scale.
It’s an exciting prospect for all with a role to play, but as Hakim Achouri, 5G Solution Architect at Airbus and Co-Chair of the GSMA 5G IoT for Manufacturing Forum pointed out, with 90% of factories still connected by Wi-Fi, there’s still a way to go – with pain points to tease out and address. Wi-Fi will doubtless continue to play a role in serving the less demanding requirements of manufacturers, but as 5G wins their trust through the ongoing proof points and trials, it will become the only choice for the most forward-looking and competitive operations. “Trust is of course vital, and we’ve really been on a steep learning curve in terms of security,” explained Bosco Novak, EVP Technology Systems at Rohde & Schwarz – “capabilities like pattern recognition, deep packet inspection, being able to act automatically, then have machine learning on top, so smart analytics can drive all this forward. Everything that requires real-time intelligence in automation needs ultra-low latency, so this is where 5G comes in.”
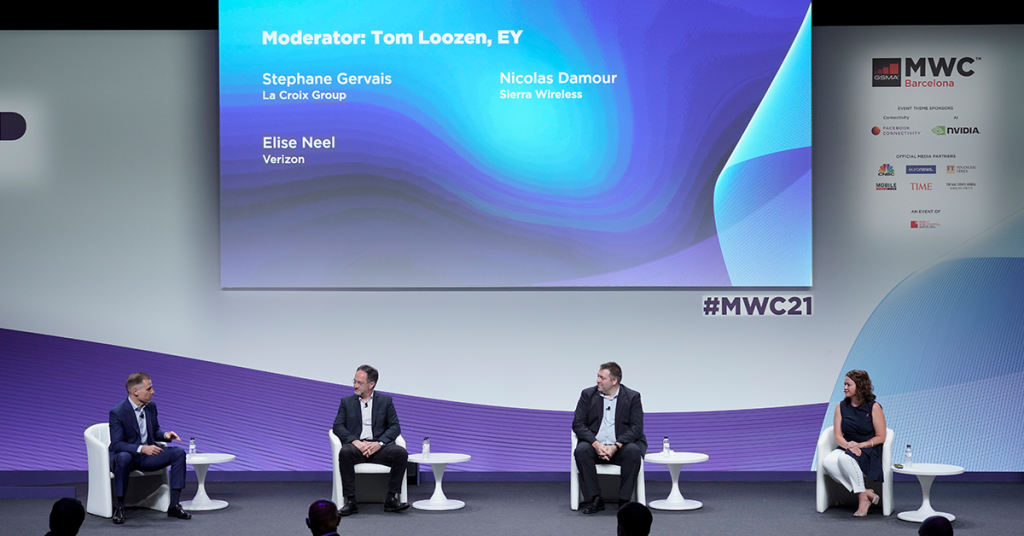
“Our research shows that 5G is the number one technology that enterprises want to invest in over the next few years,” pointed out Global Telecommunications Industry Leader at EY Tom Loozen, “with manufacturers among the highest, as network slicing comes in and starts playing a bigger role.” The key to accelerating deployment at this early stage then will be winning trust, which now looks highly promising. Next therefore comes winning confidence in a sector to whom time is money that the extra complexity will pay off via efficiencies in the long run. “Robustness, versatility, and ease of operation – these are the three pillars required to make these kinds of solutions successful,” asserted Nicolas Damour, Director of Technology Partnership Development at Sierra Wireless. This seems a sensible summation to us, and one we look forward to helping the ecosystem deliver on over the coming years, together with our leading experts from network operators such as Telefonica and Lacroix Group.
Understand the true benefits of 5G technologies applied into various Industry 4.0 applications through the GSMA resource library: https://www.gsma.com/solutions-and-impact/technologies/internet-of-things/